大型竖式炉炼镁新工艺实现升级换代
来源: 2016-02-23 12:58 点击:
次
镁合金作为21世纪最具潜力的一种结构材料,受到业界的高度关注,但其在冶炼、精炼以及合金化过程中的一系列关键问题严重制约了镁行业的健康快速发展。基于此,西安科技大学材料科学与工程学院王晓刚教授团队在理论计算与数值模拟的基础上,开展了多层次多种规模的系列试验,研发成功了大型连续式电内热法竖式炉炼镁及合金化新技术。半工业化试验取得了良好的效果,技术指标先进可靠,有望形成大型绿色高效短流程炼镁及合金化新技术与新装备,从而解决传统镁冶炼及合金化的根本性问题,为提升金属镁的冶炼及其合金化技术提供技术支撑。
镁及其合金以其优良的性能成为当今世界最受关注的新型绿色工程材料之一。中国镁产业具有良好的资源条件,已成为我国具有竞争力的可持续发展优势产业之一。随着结构轻量化技术及环保问题的需求,进一步刺激了镁及其合金工业的发展。但在镁及其合金的冶炼、精炼以及合金化过程中,存在污染严重、资源消耗大、产品纯度低、晶粒粗大以及深加工困难等一系列的问题,极大地限制了镁产业的发展。因此要将我国镁产业由生产大国提升为制造强国,必须解决产业链中的一系列关键问题。
镁冶炼的关键问题
我国原镁生产的98%以上采用皮江法,它是以煅烧白云石为原料,硅铁为还原剂,在1200℃左右进行真空热还原产生镁蒸气,并冷凝结晶成粗镁。近10余年,这种“真空还原罐间歇式”提取镁的方法,经过不断创新实践,实现了工艺和装备方面诸多卓有成效的突破,但距离高效、高质量、绿色冶金的差距还很大,仍有许多关键问题未能解决。主要表现在:环境污染严重,直接和间接排放33TCO2/TMg;还原周期过长,每个还原罐从装料到提取粗镁用时在8~10h;单罐生产能力低,平均单个还原罐的产量为20.5~22.8kg;能耗大,平均吨镁耗能4.5t标煤左右;热效率低,还原炉中,用于加热原料球团和提供反应热的能量,仅分别还原炉总能耗的3.66%和19.83%,而无效热损耗高达76.51%;还原罐体寿命短,长期处在高温含氧的环境中的还原罐使用寿命短(仅60天),不但影响生产,且成本加大;劳动强度大、作业环境差,皮江法炼镁需要人工扒渣和装料,几乎没有机械化、自动化操作;粗镁纯度有待提高,所得粗镁的主要杂质是一些蒸气压较高的金属杂质以及少量来自炉料的非金属杂质,如MgO、CaO、SiO2和Fe2O3等。尽管粗镁纯度在98%以上,但在工业应用前,仍需精炼工序。
因此,提升镁的竞争力,首先需从根本上改变镁冶炼的现状,对“真空还原罐间歇式”还原工艺及其装备进行革命性的变革。
解决方案——具有独立自主产权的“连续式电内热法竖式大型炼镁炉”装备
针对“真空还原罐间歇式”炼镁的实际情况,项目组成员经过多年不断的研究-计算-模拟-设计-实验-创制,形成了一套具有独立自主产权的“连续式电内热法竖式大型炼镁炉”的解决方案和设备,并进行了多次半工业化规模性试验,得到了较好的效果。
第一阶段为理论计算和模拟:建立在温度场叠加原理、动态表面负荷、短距离快速传热和热能高效利用原理之上,首次提出了多热源-内热式-电热法竖式炉快速炼镁方法,通过温度场的计算模拟表明,电内热法可使炉内温度场三维均匀,大幅度提高能量利用率,明显缩短还原时间。
第二阶段进行了不同反应器设计及试验:在前期计算模拟的基础上,进行了不同规格的反应器设计和试验。
第三、四阶段的试验进行了半连续性电内热法竖式炉试验、电内热法大型连续性竖式炼镁炉设计及装备设计。
“连续式电内热法竖式大型炼镁炉”解决了镁冶炼的关键问题,主要表现在炉式还原代替罐式还原,装料量可根据供电容量。该工艺理论上可无限大,结晶器可足够长,将单罐镁产量由20kg左右提高至单炉产量500kg以上,单炉产量大,实现了集约化生产。
其中,改外围加热为内部加热,实现了热源与原料的直接接触,增强了热传导效果,热利用率提高至60%以上,还原时间缩短为3h~5h,能耗明显降低。新工艺及装备,将镁冶炼的能耗由12900~13500kWh/TMg 降至 8000~10000kWh/TMg;改卧式还原系统为竖式还原结构,在重力作用下,实现半连续—连续式进出料,大幅提高生产效率,降低劳动强度;用清洁的电能源加热,摒弃污染严重的煤、气加热,控制了粉尘、烟尘及CO2、CO、SO2等温室气体和有害气体的排放,实现清洁生产。
还原出粗镁的组织致密、纯度高、损耗小,为后续精炼奠定了基础。为在距离挡火板50cm和75cm处,致密的冷凝产物层,且疏松层较薄,其纯度均在99.32~99.91wt.%以上,远高于罐式间歇式还原的粗镁纯度(98wt.%)。
实施效果显着
通过这些工作的开展,攻克传统皮江法炼镁能源消耗大、装备水平差、自动化程度低、劳动强度大、生产和产品质量不稳定、环境污染严重、资源浪费大等共性技术难题。
半工业化试验取得了先进的经济技术指标:大幅度提高冶炼炉热效率,还原时间缩短为5~6小时;能耗降低30%以上;电耗 8000~10000kWh/TMg;实现半连续-连续性热进料、热出渣、间歇式出镁的生产作业形式;镁还原率达到85%~93%,料镁比≤6.0,还原渣中MgO残余量平均在2%~5%之间,镁纯度在99.32~99.91wt.%以上;解决了煤、重油、煤气和天然气加热生产所带来的大量烟尘污染和温室气体排放问题,改善生态环境,实现还原工段的清洁生产。本技术冶炼粗镁成本约12000元/吨,经济效益好。
大型连续式电内热法炼镁发展规划
预计2016年6月底前,建成单炉装料量6吨年产1500吨镁的生产示范线,完成技术-装备-工艺-控制的全面定型。
2017年前,和国内相关企业合作,建成单炉装料12~18吨年产3万吨镁的大型示范生产线,该示范线将集新工艺、新技术与新装备一起,达到世界领先水平。
2018年在全国推广,创产值100亿元以上。
该炼镁与合金化新技术与新装备集冶炼-精炼-合金化于一体,具有短流程、高效、节能、降耗、清洁生产等优势,有望彻底改变传统炼镁与合金化作业模式,真正使镁产业成为为高新技术产业,实现炼镁技术升级换代,尽快促使我国由镁“大国”到“强国”的转变。
热门文章
相关文章
最新文章
交通路线
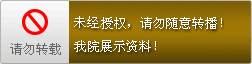